There's a lot that goes into making my timers. I start the spindles by carving wax models of each style and then making a rubber mold from the wax to cast the pewter.
After casting, the spindles are antiqued and cut to size for each of the glass timepieces, which are hand blown and filled with sand for me in England.
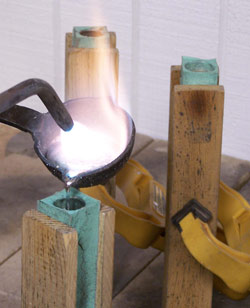
Meanwhile, select hardwoods and exotic burls are shaped, drilled, sanded, and soaked for an hour in a blend of a deep penetrating oil finish and polyurethane.
After hand rubbing to a soft luster, the wood looks natural but is now water and stain resistant.
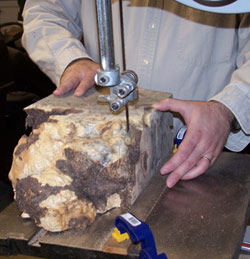
The pieces are assembled with screws and wooden plugs then sanded smooth before finishing for a second time in the oil/poly mix.
After drying on a rack for a week or so I can pack them up for shipping.
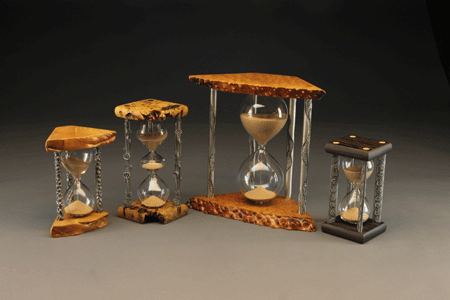

Follow us on Twitter & Facebook